Daniel Limonadi • Aug 21, 2012
Sampling Mars, Part 3: Key Challenges in Drilling for Samples
In my previous posts about the Curiosity rover's Surface Sampling and Science (SSS) system, I talked about the sampling hardware and science instruments. In this post, I'll talk about the difficulty of the work ahead of us.
First, some background. NASA has never before attempted to acquire samples by drilling on a robotic mission. Viking and Phoenix both employed scoops. During the Apollo missions, astronauts used handheld drills to acquire samples from depths of up to 2 meters. It took three generations of design before samples could be reliably acquired at the full design depth.
The Soviet space program did successfully execute robotic drilling on the Moon in the 70’s during the Luna 16/20/24 series of sample return missions. Impressively, the Soviets reportedly sampled up to 2 meters deep on the final mission in the series. In addition to the outstanding lunar results, the Soviet space program also deployed drills on several of their Venus landers, most notably the Venera 13 and 14 Venus landers. These landers reportedly had drills capable of penetrating up to 3 centimeters into rock. More recently, the European Rosetta spacecraft, launched in 2004 and on its way to a comet rendezvous in 2014, is carrying an Italian drill system (SD2) designed to penetrate up to 25 centimeters into the comet.
For the United States, the Curiosity drilling system represents a return to drilling on other bodies after a roughly 40-year hiatus. I mainly bring this up because there is a huge learning curve on the engineering team side getting people up to speed on the technical issues associated with sampling systems, especially drilling and sample processing. Just like the Entry, Descent, and Landing Team, Curiosity's sampling team has generated a very large amount of hard-won knowledge on the pitfalls, do’s, and don’ts on how to do the job correctly. This expertise is expensive to build up, and represents an investment by the country that should be protected if future sampling missions are to continue.
Drill Requirements
Key mechanical requirements on the Curiosity drill include: acquiring samples from up to 5 centimeters below the rock surface; generating a fine powder while drilling the hole to facilitate downstream sample processing for the SAM and CheMin instruments; and acquiring up to 20 science rock samples over the 2-year nominal mission.
The Curiosity drill is a powdering drill design. It does not collect intact cores. Instead, it pulverizes the rock and collects the resultant powder in a sample chamber for processing and distribution to the instruments. It does this using rotary percussive action, similar to a hammer drill you can buy at a hardware store. The main difference is that instead of just getting rid of the powder like a home drill, Curiosity's drill was designed to collect this powder through a sample tube that extends over most of the drill bit. The powder is augured up the tube using the rotating action of the drill and collected in a two-chamber sample collection area behind the bit.
Two chambers are required in order to support the ability to drill into surfaces angled up to 20 degrees from horizontal. With a five-degree-of-freedom robotic arm, we can’t control the orientation of the drill sample exit tube. As a result, we would potentially dump sample onto the ground while drilling if we did not have the sample chambers. These sample chambers have Teflon / fiberglass / molybdenum disulfide edge seals, which turned out to be a potential source of contamination for the SAM instrument. I won’t go into the details of that issue here, but maybe in a future blog entry. This powdering bit design comes at the science cost of losing the ability to view acquired intact cores, but it simplifies the overall system by removing the need for a rock crusher to pulverize the core after collection.

Processed sample requirements
The CheMin instrument works by shaking the solid sample inside its sample cells during the multi-hour X-Ray beam exposure. To do this effectively, the sample particles need to be no larger than 150 micrometers in diameter. The SAM instrument can handle larger particles, up to 1 millimeter in size. Neither system needs very much material in each sample. In the case of the 150-micrometer sample path, a single portion amounts to roughly 75 cubic millimeters. This ends up being 20 to 50 milligrams of sample, depending on the material type and its packing density inside the sample chain portioning tube. For comparison, a baby aspirin pill contains about 80 milligrams of packed powder – so our giant 100-kilogram robotic arm and sampling tools drop off the equivalent of about half of a baby aspirin pill of sample to each instrument, quite a contrast of scale!
Things That Worry Us
So, now that I have provided a little background on context and design requirements for the Curiosity Surface Sampling and Science system, what are some of the things that worry us when it comes to drilling, processing, and dropping off sample on Mars?
Is that rock going to turn into goo? In order for the Curiosity drill and the associated sample chain all the way through the instruments to work, the sample needs to act more or less like a dry, fine, powder. The system is not designed to handle wet or pasty samples. If we accidentally ingest wet or pasty samples, it might result in a temporary or permanent clog somewhere in the system.
On an extremely dry planet like Mars you might wonder why we would consider this to be a real threat. It turns out there are some mineral types, especially some of those in the sulfate and phyllosilicate (clay) mineral family, that can potentially release bound water or otherwise turn into more of a goo after drilling than a fine powder. And of course, as luck would have it, the most interesting minerals on Mars are exactly these classes of rocks which might misbehave. Based on what the MSL science team is telling us, we don’t think we are highly likely to encounter them, but it is a credible threat, and we have to guard against this given the high stakes. Clogging the sample chain would be a very bad day on Mars.
We have two ways to manage this threat. The first mitigation class is proactive. Before giving a “GO” for a drilling or scooping activity, we go through what we call a “triage” process during our sampling operations on Mars. This basically consists of collecting as much information about the target rock as possible using all the relevant instruments on the rover: the mast-mounted Mastcams, for over-all morphology and color information; the mast-mounted ChemCam instrument, for elemental chemistry; the arm-turret-mounted MAHLI hand lens imager, for fine-scale structure; and the arm-turret-mounted APXS, for elemental chemistry.
In addition to the science information from the instruments listed above, we can also use the drill to do a hardness test on the rock, or drill a shallow hole to better understand the mechanical properties of the rock before we commit to drilling a full-depth hole.
The science and engineering team compares these data to similar data we have collected during an extensive Earth-bound test campaign using copies of the flight hardware. The comparison should tell us whether we think the target rock will be okay or if it might give us trouble. If we don’t have existing data on a rock similar to what we have encountered on Mars, we might even run an analog sample through our high-fidelity test bed on Earth to practice the activity and see if there are any surprises.
Beyond this operational triage process, we also have hardware design protection. We vibrate all the sample chain surfaces to help ensure particles move where we want and when we want. (The arm-turret-mounted instruments, APXS and MAHLI, are mechanically isolated from this vibration.) And when we are done sieving our sample after instrument drop off, we basically bang our sieves against hard-stops at high speed, an activity we call "thwacking." This high-shock-force action is designed to clear material off of the sieves to keep them from blinding over time. We do this activity after every sampling activity is complete.
As you can probably tell based on this long list of things we go through as part of our triage process, planning and execution for drilling a single hole on Mars can take quite some time. It can be as fast as a few sols if everything looks obviously safe. But if the science team deems it worthwhile, we may take up to several weeks to go through the triage process for a target rock that we are nervous about.

The second mitigation class is reactive. If we find that we are not successfully clearing the sample, we will try things like doing extra thwacks and vibration to clear any clogs in the system. If that fails, we have portion poker hardware that we can use to “poke” the portion tube inside CHIMRA. None of our Earth-based testing has ever resulted in a permanent clog of the portion tube. However, we know from the Phoenix and Viking missions that Mars materials will likely throw us for a loop. The portion tube is the main choke point within the SA-SPaH parts of the sample chain, so we invested in having at least one “tool of last resort” to give us an option should it become clogged on Mars. The portion tube is about 3.5 millimeters in diameter at its exit, and the portion poker is about 2.2 millimeters in diameter.
If we have exhausted all other options and the system remains clogged, we will poke the portion tube by opening the portion door and using the arm to raster-scan the turret with the exposed portion tube onto the portion poker. This consists of moving the portion tube over the general vicinity of the portion poker (within about 2 centimeters), doing a plunging move to attempt to impale the tube, then raising the arm, moving over a few millimeters, and repeating the motion in a two-dimensional scan to ensure we get at least one good poke. The reason we have to do this 2-D scan using the arm is because the arm placement accuracy over the deck is only about 10 millimeters, so we have to try multiple times in order to ensure a hit.
Is the wind going to blow the sample away while we try to drop it off? It turns out that the particle size required by the CheMin instrument is very susceptible to being blown around by the wind on Mars. This actually happened during one of the sample drop-offs in the Phoenix mission. Phoenix attempted to deliver Organic Free Blank material (OFB) to the TEGA instrument, but the material did not make it inside. The wrist-mounted camera on Phoenix captured in stop-motion video the OFB material being blown away from the target instrument during the drop-off attempt. This was rather disappointing for the operations team, a case of bad luck doing that drop-off on a relatively windy day.
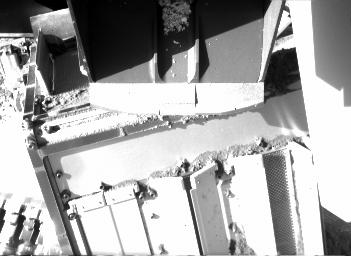
On Curiosity we have several hardware and operational schemes to help mitigate this. We have rover- and turret-mounted “wind guard” hardware that is designed to help provide aerodynamic shielding to the sample during drop-off. In addition, we hope to use data from the Spanish REMS weather station that is carried by Curiosity to get insight into the wind speed and direction trends for where the rover is currently located. If the wind speed is significant, say greater than 5 meters per second (about 11 miles per hour), and/or is coming from a direction that the wind guard hardware does not perform well in, the operations team might pick a different time of day and/or orient the rover to help better mitigate the wind threat during sample drop-off to the instruments.
We can also drop off more than one sample to each instrument in order to mitigate the effects of sample loss due to wind. However, this has the downside of increasing the uncertainty of delivered mass, and at least for the SAM, this makes it harder for the instrument team to report on the actual concentration of volatiles in the delivered sample (i.e. if you have an uncertainty in delivered mass of a factor of 2-4 then you can only report on volatile concentrations within the same error bar).
Is that rock going to move? In order to stabilize the arm and rock for the drilling operation, the Curiosity robotic arm is designed to preload the drill against the rock with a minimum of about 300 Newtons of force. But to ensure this minimum force, we might apply a preload to the rock as high as 400 Newtons or more (this is close to 100 pounds of force: there are 4.45 Newtons per 1 pound force). For vertical or bedrock drilling activities, we don’t need to worry as much about the size of the rock, though the rock still needs to be large enough to accommodate the drill contact prongs with some margin, and if we have a rock sitting on soft regolith it might need to be relatively large to avoid sinking during the drilling activity. However, when the science team wants to drill horizontally or with any significant horizontal component, we have to look at the rock and guess at how well it might be anchored in the terrain or how heavy it might be before we can give a green light for drilling. If we determine that the rock is important but we aren’t sure the rock can support the force required for drilling, we have the option of pushing on the rock with the arm/drill combo to see if it stays put, crumbles, or moves before committing to the actual drilling operation.
Is the rover going to slip while we are at this location? Curiosity is much larger than Spirit and Opportunity, and has an aluminum chassis, compared to the Spirit / Opportunity rovers, which have a carbon-fiber composite chassis. An interesting side effect of these seemingly mundane differences is that during the diurnal 100 degrees Celsius thermal swing, the rover aluminum chassis and titanium mobility system end up growing and shrinking a total of roughly 4 millimeters (about one sixth of an inch). It might not seem like it, but this is a pretty big number! It is big enough to make us worry about vehicle stability from one sol to the next if we are on terrain that might pose a slip risk – e.g. being on a significant tilt, on “slippery” terrain like flat bedrock, or even not-so-slippery terrain if it has lots of little bumps where the wheels might slip off of during the diurnal cycle.
Why do we care if we slip? If the arm has not placed any turret tools into contact with the ground then we generally don’t worry about it. However, if the drill is on or in a rock or other tools are in contact with regolith or rocks we need to think through whether or not we might slip and whether any hardware might be damaged if the rover does slip. It is relatively easy for us to figure out what the damage threat is from a certain fixed magnitude of slip, but it is very difficult to judge whether we think we will actually slip enough to cross a damage threshold. It is important to note that we will always slip a little given the huge forces put out by thermal expansion and contraction of the hardware.
So, what do we do? Early in the mission, while we are characterizing how the vehicle behaves on Mars at temperature (roughly the first 3 months or so) we will restrict ourselves to sampling operations at tilts below about 7 degrees and will stay off anything that we think poses a high slip risk. As we get data from rover operations and how the vehicle actually behaves on the Martian surface, we will open up the envelope to the full 20 degrees for sampling and 30 degrees for contact science activities (contact science is just using the DRT, MAHLI, and APXS on surface targets, like what Spirit and Opportunity did with their robotic arms).
Stay tuned for the final part in this series: Commissioning the Rover and Sampling System
Support our core enterprises
Your support powers our mission to explore worlds, find life, and defend Earth. You make all the difference when you make a gift. Give today!
Donate